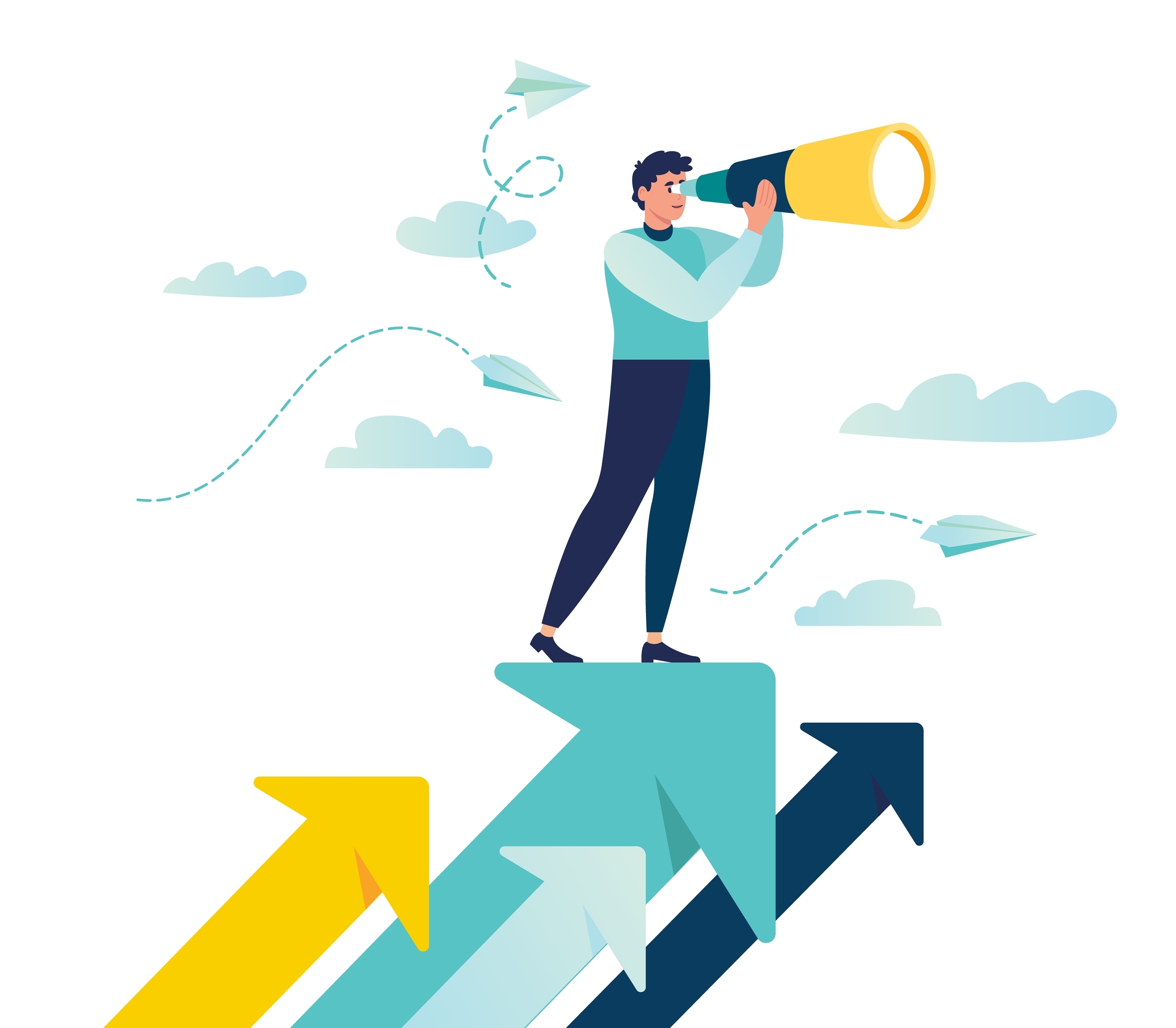
While tariff policies remain a moving target, many manufacturers aren’t waiting to react. They’re already adapting their supplier relationships, material strategies, and production setups to stay resilient — regardless of what’s announced next.
In industries like food and beverage, where safety, speed, and compliance are non-negotiable, building flexibility into packaging and coding operations is now essential. Here’s how forward-thinking brands are preparing.
Stay ahead with real-time updates on the latest news:
Six strategies manufacturers use to stay resilient amid trade uncertainty
Manufacturers are adjusting packaging strategies across food, beverage, and consumer goods to manage rising material costs, unpredictable tariffs, and supply chain risks. These six strategies demonstrate how resilient businesses adapt to these challenges.
- Rethink packaging materials: To reduce exposure to tariffs and supply disruptions, brands are exploring locally sourced or lower-tariff materials. For example, switching from imported coated paperboard to domestic fiber-based or compostable cartons can not only help minimize risk but support sustainability goals, a potential win for both the bottom line and a brand’s image.
- Diversify supplier network: Utilizing multiple suppliers, including domestic options, can enhance resilience against market disruptions and tariff changes. Diversifying sources may result in cost savings by enabling competitive pricing and reducing overall expenses.
- Renegotiate and rebalance supplier terms: With costs in flux, many manufacturers are revisiting contracts to secure better pricing or more flexible terms. In some cases, these companies are locking in longer-term pricing or adjusting order sizes to better manage costs and attain supply chain stability.
- Invest in lean and connected operations: Streamlining production with smarter tools helps brands stay efficient and responsive. Videojet customers using IIoT-connected systems, for instance, can identify slowdowns, reduce changeover time, and access remote troubleshooting — all while minimizing unplanned downtime.
- Reassess in-house vs. outsourcing: As sourcing risks shift, so do manufacturing strategies. Some manufacturers are bringing critical packaging steps in-house for more control, while others are outsourcing to trusted partners in tariff-friendly regions. In-house production offers greater control over quality and lead times, while outsourcing can leverage external expertise and economies of scale.
- Keep up with regulations: Packaging and coding rules change quickly, from recyclability standards to traceability mandates. Brands that build compliance into their packaging workflows avoid delays and costly rework, especially when introducing new materials or sourcing from new suppliers.
Code with confidence on any packaging material
No matter how your packaging strategy changes, codes on your packages need to be clear and compliant. Flexible systems like those from Videojet are designed to consistently print on the full range of packaging materials, from glass and foil to cardboard and compostable film — even on ultra-high-speed lines and in complex productions setups. For products that require traceability, these systems help ensure that codes are accurate and reliable.
Videojet coding and marking systems are built for flexibility — adapting to different substrates, packaging types, and production requirements. With tools like VideojetConnect™ and CLARiSUITE®, you can remotely manage, monitor, and automate your printing operations while supporting lean manufacturing and helping to reduce downtime. Whether your packaging strategy shifts or your supply chain evolves, your coding systems will keep up.